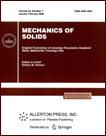 | | Mechanics of Solids A Journal of Russian Academy of Sciences | | Founded
in January 1966
Issued 6 times a year
Print ISSN 0025-6544 Online ISSN 1934-7936 |
Archive of Issues
Total articles in the database: | | 13205 |
In Russian (Èçâ. ÐÀÍ. ÌÒÒ): | | 8140
|
In English (Mech. Solids): | | 5065 |
|
<< Previous article | Volume 58, Issue 1 / 2023 | Next article >> |
X. Zhang, X.C. Yin, J.Q. Lv, and W. Li, "A Modal Displacement Unevenness Coefficient Method for Multi-Point Matrix Damage Detection in Composite Laminates," Mech. Solids. 58 (1), 366-380 (2023) |
Year |
2023 |
Volume |
58 |
Number |
1 |
Pages |
366-380 |
DOI |
10.3103/S0025654422601586 |
Title |
A Modal Displacement Unevenness Coefficient Method for Multi-Point Matrix Damage Detection in Composite Laminates |
Author(s) |
X. Zhang (Tiangong University, Tianjin, 300387 China; School of Aeronautics and Astronautics, Tianjin, 300387 China, zhangxu@tiangong.edu.cn)
X.C. Yin (School of Aeronautics and Astronautics, Tianjin, 300387 China)
J.Q. Lv (School of Aeronautics and Astronautics, Tianjin, 300387 China)
W. Li (Tianjin Chengjian University, Tianjin, 300384 China; School of Energy and Safety Engineering, Tianjin, 300384 China) |
Abstract |
The matrix cracking severely decreases the load-bearing performance of composite laminates even though its smaller degree in comparison with delamination, cut-out, and hole. The initial parameters in modal analysis, such as natural frequency, modal displacement, and modal curvature, can only detect a damage with large changes in geometric shape and elastic modulus. To solve this situation, a new Non-Destructive Testing (NDT) method using the power function of modal curvature difference is developed to identify the multi-point matrix damage. The Camanho damage criterion is adopted to construct the matrix compression failures in multiple locations, and the finite element models are established for undamaged and damaged laminates with different fiber angles. The force hammer excitation experiment is performed on undamaged carbon fiber laminates, and the modal displacements of measuring points, obtained by Dong-Hua Data Analysis System (DHDAS), are compared with numerical results. Considering the simulation provides enough measuring points to precisely characterize the abrupt characteristics of the curved surface, the numerical mode shape is adopted to calculate the Gaussian curvature. The square of Gaussian curvature difference between undamaged and damaged laminates is defined as the unevenness coefficient, and its variations with the location and number of matrix damage are studied for single- and multi- order modes. Simultaneous and high-accuracy detection of multi-point matrix failure is realized in this process, confirming that the presented method is a valuable tool for detecting the damage of composite laminates. |
Keywords |
composite laminates, multi-point matrix damage, modal analysis, non-destructive testing |
Received |
26 October 2022 | Revised |
07 November 2022 | Accepted |
08 November 2022 |
Link to Fulltext |
|
<< Previous article | Volume 58, Issue 1 / 2023 | Next article >> |
|
If you find a misprint on a webpage, please help us correct it promptly - just highlight and press Ctrl+Enter
|
|