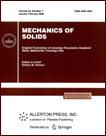 | | Mechanics of Solids A Journal of Russian Academy of Sciences | | Founded
in January 1966
Issued 6 times a year
Print ISSN 0025-6544 Online ISSN 1934-7936 |
Archive of Issues
Total articles in the database: | | 13217 |
In Russian (Èçâ. ÐÀÍ. ÌÒÒ): | | 8152
|
In English (Mech. Solids): | | 5065 |
|
<< Previous article | Volume 57, Issue 2 / 2022 | Next article >> |
K. S. Bormotin, A. A. Burenin, and A. A. Krivenok, "On the Optimization of the Kinematic Scheme for Shaping thin Elastoplastic Coverings," Mech. Solids. 57 (2), 214-222 (2022) |
Year |
2022 |
Volume |
57 |
Number |
2 |
Pages |
214-222 |
DOI |
10.3103/S0025654422020030 |
Title |
On the Optimization of the Kinematic Scheme for Shaping thin Elastoplastic Coverings |
Author(s) |
K. S. Bormotin (Komsomolsk-na-Amure State University, Komsomolsk-na-Amure, Khabarovsky Kray, 681013 Russia, cvmi@knastu.ru)
A. A. Burenin (Institute of Machinery and Metallurgy of the Far Eastern Branch of the Russian Academy of Sciences, Komsomolsk-na-Amure, Khabarovsky Kray, 681105 Russia, aab@imim.ru)
A. A. Krivenok (Komsomolsk-na-Amure Aircraft Plant Named After Yu. Gagarin, Komsomolsk-na-Amure, Khabarovsky Kray, 681018 Russia, baikal-190@yandex.ru) |
Abstract |
One of the ways to obtain parts of aircraft structures is the sheet stretching process. The accuracy of manufacturing parts by the sheet stretching method is influenced by such technological conditions of the forming process as the geometry of the punch and the kinematics of the control bodies of the sheet stretch press. The article discusses the modeling of the process of forming a sheet by punch stretching and optimization of the trajectory of movement of the clamps of the sheet stretch press. A numerical method has been developed for solving the problems of optimal control of the sheet stretching process. The values of residual displacements and material damage in ductility are considered as an optimization criterion. Based on the discrete formulation of the optimal control problem, the dynamic programming method is implemented. The space of solutions to optimization problems, developed by the methods, includes both monotonic and non-monotonic deformation trajectories, taking account of partial unloading. In the case of analysis of non-monotonic deformation trajectories, an elastoplastic material with isotropic, kinematic, and combined hardening is considered. Algorithms implemented in well-known engineering analysis programs allow calculating the optimal operating parameters of sheet stretch press with a programmable numerical control. The simulation results are compared with full-scale experiments on the sheet parts stretching on a special sheet stretch press. |
Keywords |
elasticity, plasticity, sheet stretching, residual displacements, damage, finite element method, optimal control, dynamic programming |
Received |
17 October 2021 | Revised |
20 October 2021 | Accepted |
21 October 2021 |
Link to Fulltext |
|
<< Previous article | Volume 57, Issue 2 / 2022 | Next article >> |
|
If you find a misprint on a webpage, please help us correct it promptly - just highlight and press Ctrl+Enter
|
|