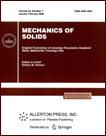 | | Mechanics of Solids A Journal of Russian Academy of Sciences | | Founded
in January 1966
Issued 6 times a year
Print ISSN 0025-6544 Online ISSN 1934-7936 |
Archive of Issues
Total articles in the database: | | 13217 |
In Russian (Èçâ. ÐÀÍ. ÌÒÒ): | | 8152
|
In English (Mech. Solids): | | 5065 |
|
<< Previous article | Volume 43, Issue 3 / 2008 | Next article >> |
V. N. Kukudzhanov and A. L. Levitin, "Numerical modeling of cutting processes for elastoplastic materials in 3D-statement," Mech. Solids. 43 (3), 494-501 (2008) |
Year |
2008 |
Volume |
43 |
Number |
3 |
Pages |
494-501 |
DOI |
10.3103/S0025654408030205 |
Title |
Numerical modeling of cutting processes for elastoplastic materials in 3D-statement |
Author(s) |
V. N. Kukudzhanov (Institute for Problems in Mechanics, Russian Academy of Sciences, pr-t Vernadskogo 101, str. 1, Moscow, 119526, Russia, kukudz@ipmnet.ru)
A. L. Levitin (Institute for Problems in Mechanics, Russian Academy of Sciences, pr-t Vernadskogo 101, str. 1, Moscow, 119526, Russia, alex_lev@ipmnet.ru) |
Abstract |
In the present paper, we use the finite element method to perform the three-dimensional modeling of unsteady process of cutting an elastoplastic plate (slab) by an absolutely rigid cutting tool moving at a constant velocity V0 at different inclinations α of the tool face (Fig. 1). The modeling was based on the coupled thermomechanical model of an elastoviscoplastic material. The adiabatic process of cutting was compared with the regime in which the slab material heat conduction is taken into account. The cutting process was parametrically studied for variations in the slab and cutting tool geometry, in the rate and depth of cutting, and in the properties of the processed material. The slab thickness was varied in the direction of the axis z. The stressed state varied from the plane-stressed H=H/L «1 (thin plate) to the plane-strained H »1 (wide plate), where H is the slab thickness and L is the slab length. The problem was solved on a moving adaptive Lagrange-Euler grid by the finite element method with splitting, by using the explicit-implicit integration schemes for equations [13]. It was shown that the numerical modeling of the problem in the three-dimensional statement permits studying the cutting processes with continuous chip formation and with chip destruction into separate pieces. The mechanism of this phenomenon in the case of orthogonal cutting (α=0) can be explained by the thermal softening with formation of adiabatic shear strips without using the damage models. In cutting by a sharper tool (the angle α is large), it is necessary to use the coupled model of thermal and structural softening. We obtain dependences of the force acting on the tool for different geometric and physical parameters of the problem. We also show that the quasimonotone and oscillating operation modes are possible and explain them from the physical standpoint. |
Received |
25 February 2008 |
Link to Fulltext |
|
<< Previous article | Volume 43, Issue 3 / 2008 | Next article >> |
|
If you find a misprint on a webpage, please help us correct it promptly - just highlight and press Ctrl+Enter
|
|