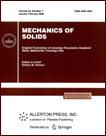 | | Mechanics of Solids A Journal of Russian Academy of Sciences | | Founded
in January 1966
Issued 6 times a year
Print ISSN 0025-6544 Online ISSN 1934-7936 |
Archive of Issues
Total articles in the database: | | 13217 |
In Russian (Èçâ. ÐÀÍ. ÌÒÒ): | | 8152
|
In English (Mech. Solids): | | 5065 |
|
<< Previous article | Volume 59, Issue 2 / 2024 | Next article >> |
Jing Gao, Zhaopeng Xu, Runyi Han, Zichen Qi, and Guang Han, "Refinement of Hyperelastic Models Based on Tension and Compression Experiments of Polydimethylsiloxane (PDMS)," Mech. Solids. 59 (2), 955-965 (2024) |
Year |
2024 |
Volume |
59 |
Number |
2 |
Pages |
955-965 |
DOI |
10.1134/S0025654424602659 |
Title |
Refinement of Hyperelastic Models Based on Tension and Compression Experiments of Polydimethylsiloxane (PDMS) |
Author(s) |
Jing Gao (Hebei Key Laboratory of Microstructure Materials Physics, College of Science, Yanshan University, Qinhuangdao, 066004 China, gaojing986@126.com)
Zhaopeng Xu (College of Information Science and Engineering, Yanshan University, Qinhuangdao, 066004 China)
Runyi Han (College of Information Science and Engineering, Yanshan University, Qinhuangdao, 066004 China)
Zichen Qi (College of Information Science and Engineering, Yanshan University, Qinhuangdao, 066004 China)
Guang Han (Department of Mechanical and Electrical Engineering, Hebei Construction Material Vocational and Technical College, Qinhuangdao, 066004 China) |
Abstract |
Polydimethylsiloxane (PDMS) has attracted more attention due to its excellent elasticity and biomedical compatibility, can be applied in the design and manufacture of actuators, sensors and medical devices. In order to better simulate the tensile and compressive process of PDMS and obtain more accurate simulation results, multiple hyperelastic constitutive models based on PDMS materials were investigated. Firstly, according to the strain energy density function in the hyperelastic theory, engineering stress expressions for uniaxial deformation were derived in terms of Mooney–Rivlin with five parameters model and Yeoh model, as well as Mooney–Rivlin with two parameters model, Neo-Hookean model and Ogden model were all organized. PDMS samples were prepared with mixing ratio of 10:1 of base polymer and curing agent, dried at 60°C, and then we acquired the deformation values varying with tensile force and pressure. Afterwards, various material models were modelled with COMSOL Multiphysics, and the optimal material parameters of hyperelastic models for tensile, compressive, both tensile and compressive experimental data were analyzed, respectively. The results reveal that Mooney–Rivlin with five parameters models exhibit excellent fitting effect, with different material parameters for these three cases, as well as the determination coefficients of goodness of fit all greater than 0.99. Certainly, other hyperelastic models also have their own characteristics, Mooney–Rivlin with five parameters model especially has prominent advantage in simulating the stress-strain process of PDMS. In summary, the developed research findings provide valuable references into the accurate modeling of PDMS behavior, with practical significance for engineering application. |
Keywords |
PDMS elastomer, hyperelastic model, tension and compression, COMSOL Multiphysics, goodness of fit |
Received |
05 February 2024 | Revised |
12 March 2024 | Accepted |
16 April 2024 |
Link to Fulltext |
|
<< Previous article | Volume 59, Issue 2 / 2024 | Next article >> |
|
If you find a misprint on a webpage, please help us correct it promptly - just highlight and press Ctrl+Enter
|
|