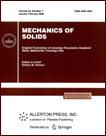 | | Mechanics of Solids A Journal of Russian Academy of Sciences | | Founded
in January 1966
Issued 6 times a year
Print ISSN 0025-6544 Online ISSN 1934-7936 |
Archive of Issues
Total articles in the database: | | 13276 |
In Russian (Èçâ. ÐÀÍ. ÌÒÒ): | | 8152
|
In English (Mech. Solids): | | 5124 |
|
<< Previous article | Volume 42, Issue 1 / 2007 | Next article >> |
V. I. Agal’tsov, S. A. Vladimirov, and V. P. Degtyarev, "Mathematical modeling of mechanical properties of metals and alloys at large strains," Mech. Solids. 42 (1), 123-134 (2007) |
Year |
2007 |
Volume |
42 |
Number |
1 |
Pages |
123-134 |
Title |
Mathematical modeling of mechanical properties of metals and alloys at large strains |
Author(s) |
V. I. Agal’tsov (Central Research Institute of Machine Building Russian Space Agency, Pionerskaya 4, Korolev, Moscow reg., 141070, Russia, centev5@tsniimash.ru)
S. A. Vladimirov (Central Research Institute of Machine Building Russian Space Agency, Pionerskaya 4, Korolev, Moscow reg., 141070, Russia)
V. P. Degtyarev (Central Research Institute of Machine Building Russian Space Agency, Pionerskaya 4, Korolev, Moscow reg., 141070, Russia) |
Abstract |
We discuss problems in mathematical modeling of the mechanical behavior of metals and alloys at large strains. Attention is mainly paid to the analysis of the stress-strain state of specimens and structural fragments made of highly plastic materials with the effect of stability loss under tensile stresses taken into account. We discuss the methods for determining the true property diagram at strains exceeding the ultimate uniform strain. We process experimental data and determine the true property diagrams for AMg6, AMg6M, and 1201 aluminum alloys and BrKh08 alloy.
To calculate the load-carrying capacity of structural members, one often uses the conventional ultimate strength σb accepted in regulations as a material characteristic. But it follows from the method for experimentally determining this characteristic that it depends on the properties of the specimen viewed as a structure. As a result, a formal use of fracture criteria recommended in regulations leads to a discrepancy between design and experimental values of fracture loads.
Nowadays, the finite element method is widely used in practical strength analysis. This method permits one to study the elastoplastic strained state of geometrically complicated structures in detail, take into account physical nonlinearity at large strains, determine damage boundaries, and improve experimental methodology. The wide capabilities of this method allow one to use test results more completely. |
References |
1. | A. A. Il'yushin,
Plasticity
(Gostechizdat, Moscow, 1948)
[in Russian]. |
2. | K. J. Bathe,
Finite Element Procedures
(Prentice Hall, Englewood Cliffs, HJ, 1996). |
3. | V. P. Degrtyarev, Strain and Fracture in Highly Stressed Structures
(Mashinostroenie, Moscow, 1987) [in Russian]. |
4. | F. McClintock and A. Argon,
Mechanical Behavior of Materials
(Mir, Moscow, 1970)
[in Russian]. |
5. | N. N. Malinin, Applied Theory of Plasticity and Creep
(Mashinostroenie, Moscow, 1968) [in Russian]. |
6. | V. P. Kogaev, N. A. Makhutov, and A. P. Gusenkov, Strength and
Durability Analysis of Machine Parts and Structural Members
(Mashinostroenie, Moscow, 1985) [in Russian]. |
7. | M. P. Markovets, True Stress Diagrams and Strength Analysis
(Oborongiz, Moscow, 1947) [in Russian]. |
|
Received |
16 June 2004 |
Link to Fulltext |
|
<< Previous article | Volume 42, Issue 1 / 2007 | Next article >> |
|
If you find a misprint on a webpage, please help us correct it promptly - just highlight and press Ctrl+Enter
|
|